Celebrating Safety: Portland Marks 8 Years, Saginaw Surpasses 1 Million Hours with ‘No Days Away’
Workplace safety milestones at two manufacturing plants underscore Northwest Pipe’s commitment to employee health and safety.
In early August, employees at NWP’s Portland Plant took a day off from their regular duties to participate in their annual “Safety Day.” At this year’s event, the team had a major milestone to celebrate: 8 years with “no days away.” This safety streak marks an all-time record for the Company.
To Diane Ishimwe, Portland’s Health and Safety Coordinator, the 8-year record serves as both an achievement and a continued motivation to “Keep working together to have a safe workplace.” For the Portland plant, she says, “This demonstrates a team effort to maintain a safe work environment and a culture of safety awareness from the frontline employees to the highest level of management.”
That culture of safety awareness is cultivated through a comprehensive safety program, which includes an on-site safety committee, job safety analysis and accident investigation procedures, Safety Grams, and a two-pronged approach to safety training consisting of initial training and ongoing refresher training. Initial training is required of new employees and those starting new tasks. Refresher training varies in subject matter and frequency, and focuses on promoting continued learning, increasing confidence and hazard awareness, and reducing errors.
The annual Safety Day is an important part of refresher training at all NWP plants. At this year’s Safety Day, the Portland plant welcomed outside vendors to lead hands-on training on a variety of topics, including:
- Lock Out/ Tag Out training (Presented by Grainger/Brady Corporation)
- Hazard Communication training (Presented by Grainger/Brady Corporation)
- Slings and chains safety (Presented by Pope Rigging Loft)
- Fire extinguishers hand-on training (Presented by Metro Safety and Fire)
- Fall protection and ladder safety training (Presented by Airgas)
Additionally, lean manufacturing training was provided by Portland’s Lean Coordinator, Michael Robbins.
Proper maintenance on tools and machinery also plays a critical role in creating a safe manufacturing workplace. “Following lock out/tag out procedures, regular inspections, and other regularly scheduled tasks help in reducing equipment failure, increasing system reliability and reducing injuries,” says Diane.
At the NWP plant in Saginaw, Texas, they recently hit a safety milestone of their own, surpassing 1 million hours without a time lost accident. Saginaw’s Safety and Environmental Manager, Les Lowe, attributes the accomplishment to a collaborative team effort. “It took all of us; management, supervision, and employees to achieve this milestone,” states Les. “It’s not about a number, it’s about people. We want all to go home safe to our families. We look out for each other.”
Les says the fundamental method of protecting employees is controlling exposures to occupational hazards. He refers to a Hierarchy of Controls to help determine how to implement and control solutions, a practice he simplifies as, “Do the basics, repeat, and then repeat again…”
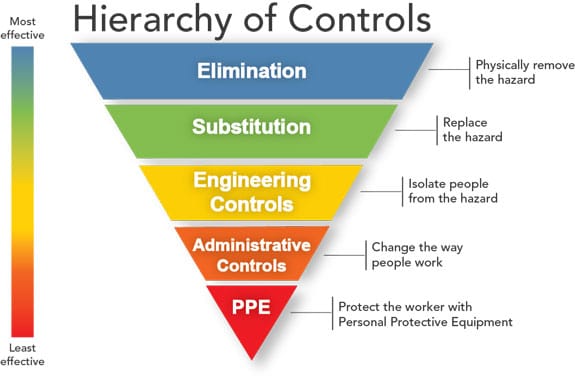
The success of the safety program at Northwest Pipe goes beyond training: it takes employee input, participation, and vigilance to create and maintain a safe working environment. Encouraging employee involvement in safety initiatives is the PIT (Process Improvement Team) program, which asks plant employees to submit their ideas for improving safety, product quality, and equipment/process reliability. A quarterly cash incentive keeps the ideas flowing in, and the PIT program currently has a 100% participation rate across all plants. With $128,000 budgeted for cash prizes this year, Northwest Pipe’s investment in the PIT program represents a commitment to safety from executive management all the way to the plant floor.
“It starts with our CEO, he cares deeply about the safety of our employees,” says Matt Baker, Vice President of Manufacturing Resources and Reliability and the designer of the PIT program. “Our culture is being engaged with and listening to our employees, and challenging our employees if they are doing anything unsafe. Similarly, our goal is for employees to respectfully challenge one another when they see safety issues.” Alluding to the ACT value of accountability, Matt continues, “Everybody holds everybody accountable for safety.”
Employee-driven process improvements and a culture of accountability are major contributing factors in Northwest Pipe’s industry-leading safety rates. In 2020, NWP’s recordable incident rate and “days away” were well below the industry average for steel pipe manufacturers.
At Saginaw, safety rates represent something more than just a number. “Meeting compliance standards means achieving the minimal standards. We don’t want minimal,” declares Les. “Our goal and passion is for all to go home safe to our families. Ongoing/refresher training is conducted to achieve our goal and passion.”
A passion for safety is evident in the major milestones recently reached at the Portland and Saginaw plants. Commending their major accomplishments, Matt asserts, “It shows their commitment to safety and willingness to ensure a safe working environment for all employees.” It’s also indicative of Northwest Pipe’s greater goal for safety as a Company. “Our roadmap is employee engagement,” continues Matt. “If every employee challenged one another when they saw something unsafe, we wouldn’t need safety programs, and I’d be out of a job. That’s the goal.”