Permalok® HDD Pipe Crosses NYC’s East River for Landmark Renewable Energy Project
Over 10,000 Feet of Steel Casing Pipe with Permalok® HDD Joints Connects a Critical Subterranean Segment of New York’s Champlain Hudson Power Express Project.
The Champlain Hudson Power Express (CHPE) is a buried transmission line designed to deliver hydroelectric power from Canada to the New York metropolitan area. CHPE supports the state’s sustainability goal of sourcing 70% of energy from renewable sources by 2030. The 339-mile-long project starts at the US-Canada border, traveling south through Lake Champlain, under the Hudson River, and finally, crossing the East River to end at a new converter station in Astoria, Queens. Northwest Pipe Company is supplying 10,400 feet of 20-inch steel casing pipe with Permalok HDD® joints for the final segment of this project. Installed in two parallel 5,200-foot drives under the East River, the HDD pipeline will house fusible PVC carrier pipe for the project’s fiber optic cables, connecting Randall’s Island and the Astoria converter station. Kiewet is the contractor on the project and Michels is the subcontractor for this trenchless segment.
Project Design
This segment of the project is being installed via Horizontal Directional Drilling (HDD), a trenchless application in which pipe is drilled at an angle from a rig staged at surface level. This method minimizes surface disruptions and the environmental impact of construction while allowing for pipe to be installed safely under waterways and around existing utilities. The HDD method was selected due to the depth of the East River, and the project was originally designed to have a pipe string out on Randall’s Island. However, due to space constraints of the urban setting, including train crossings, highway overpasses, and a popular sports complex and recreational facilities in the area, pipe string out was not feasible, and an approach utilizing a smaller footprint was needed.
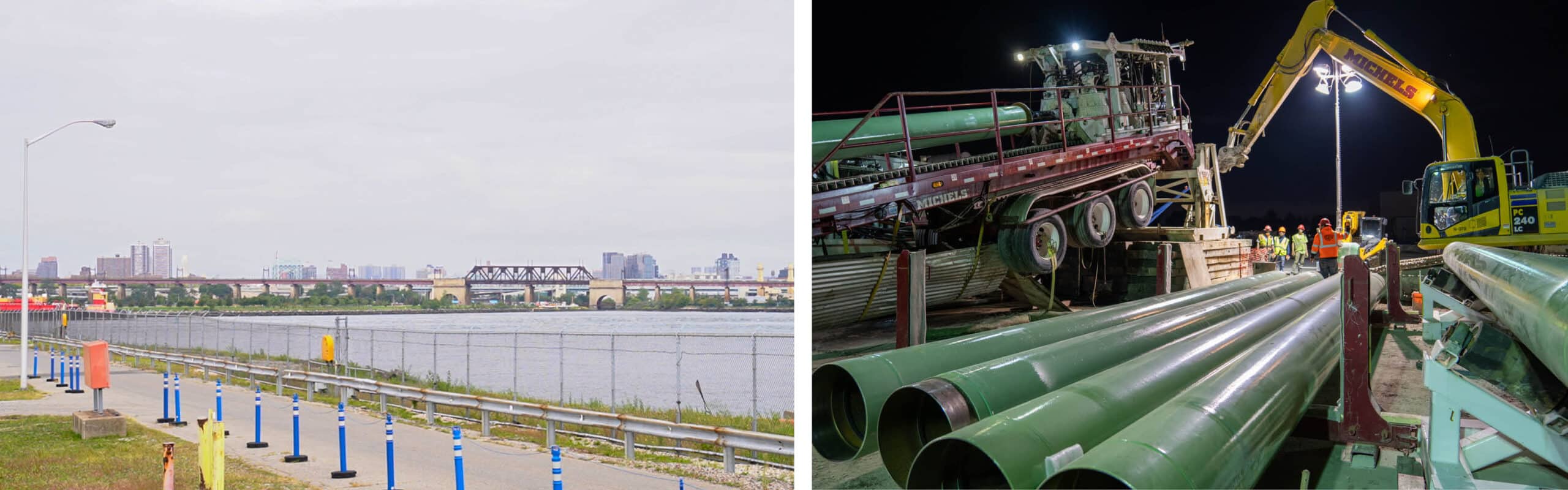
To address these constraints, Michels reached out to Northwest Pipe Company about using the Permalok® HDD joint. The Permalok® HDD is a weld-free solution that allows for the casing pipe to be cartridge-fed from the launch rig side, eliminating the need for string out on the exit side. The Northwest Pipe trenchless team collaborated closely with Michels and the project engineer through the project design process. In the next phase, Northwest Pipe provided Permalok® HDD joints for testing at the Michels facility in Wisconsin to verify the performance of the pipe connections against the project’s demanding specifications.
Manufacturing
The pipe was manufactured in 30-foot sections at Northwest Pipe’s Permalok plant in St. Louis, Missouri. A total of 345 sections of pipe were produced, each with a patented HDD joint ring welded to either end. The joint rings are precision-machined to a 0.005-inch tolerance. Each pipe undergoes a comprehensive quality assurance process, including checks for consistent length, roundness, and joint ring straightness, which is documented in a QA record maintained for each pipe supplied to the job. The sections were coated per project specifications and shipped on time to the jobsite.
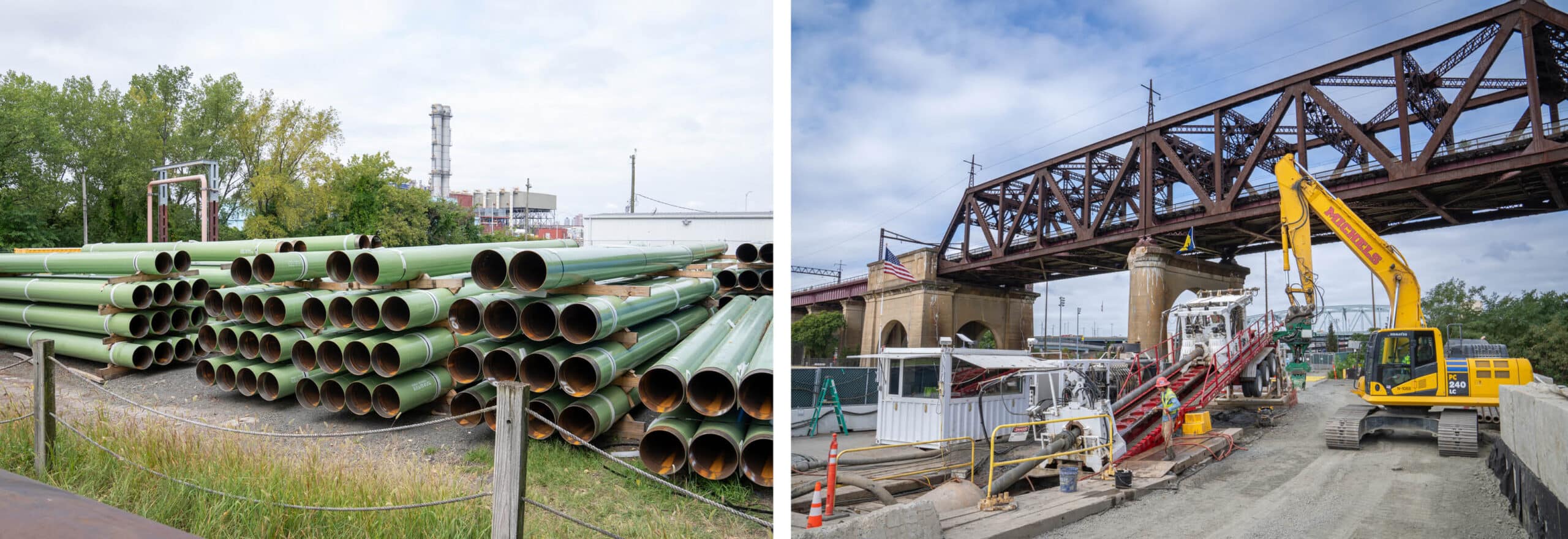
HDD Installation
To prepare for the HDD pipe installation, Michels crews began by drilling two pilot bores, starting at 12-inch diameter and upsizing to 34 inches. The bores extend from the onshore launch rig at the Astoria converter station, 150 feet below the East River, to an exit rig on Randall’s Island. The first Permalok HDD joint was welded to a 120-feet section of uncoated steel casing, designed to absorb the vibration created by the spinning pull head. The pull head is used to guide the HDD pipe along the pilot bore path as it advances. Built by the Michels team, the drill rig utilizes a hydraulic press to push the pipe into the pilot bore. The Permalok® HDD Joint features a compression-fit interlocking design that securely connects with no field welding required. The joint profile incorporates an additional locking key on the male connection side to increase pull-apart resistance while requiring less force to push joints together.
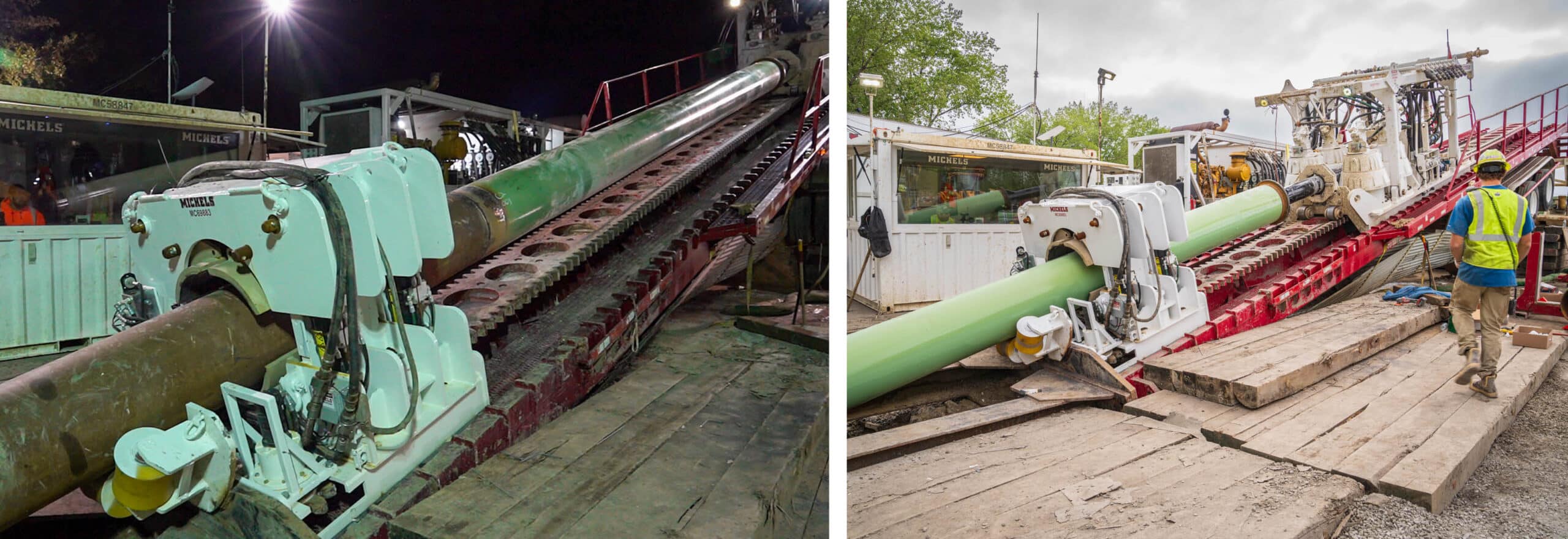
Once the first Permalok pipe joint was advanced, the next was placed into the drill rig and carefully aligned with the end of the first joint. A hydraulic clamp, custom-designed and fabricated by the Michels team, was set up at the base of the drill rig to help keep the pipe aligned while the next pipe was being fed into the rig. The ends were then pushed together until the joint fully engaged, and the connected pipe was advanced along its path under the river. The first few joints required some exploration time, but crews quickly found a rhythm and were soon connecting joints within minutes.
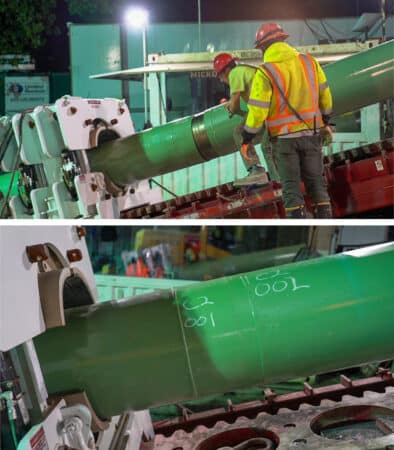
Advantages in Speed & Efficiency
The Permalok HDD joint system significantly streamlined the installation process by eliminating the need for pipe string-out and on-site welding, providing a distinct advantage over traditional HDD pipe. Jeremiah Yliniemi, Assistant Operations Manager at Michels, notes, “It’s a simple process for a complex project. The Permalok HDD joint is very easy to work with and installs much faster and more efficiently than welding traditional HDD pipe strings.” The enhanced ease and speed of installation translates to reduced project costs, says Yliniemi. “The biggest cost savings are on welding crews and other equipment needed for pipe string layout and pullback assistance, plus it can all be done on the space you are already using.”
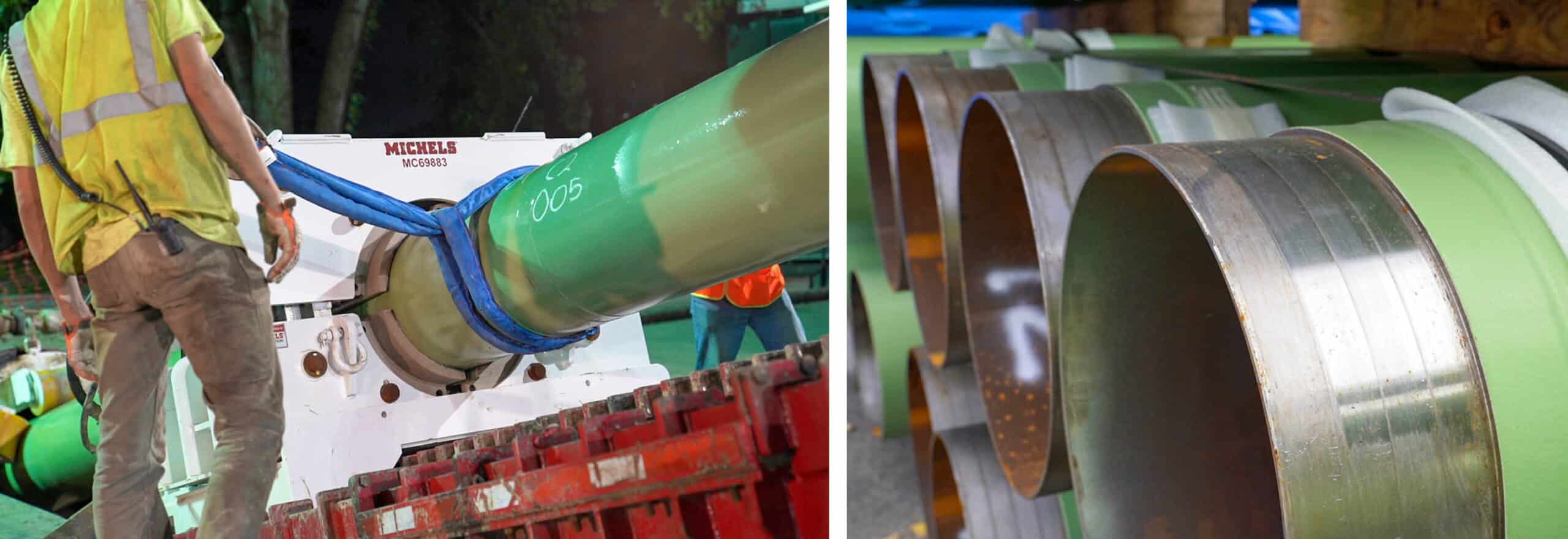
The dedicated Michels team worked around the clock to complete the installation in a tight timeline. They completed the first 5,200-foot drive in less than 2.5 days, averaging an impressive pace of 100 feet per hour (including breaks for the construction crew). The second drive was completed even more rapidly, showcasing the efficiency of the Permalok® HDD joint system.
Project Support
Northwest Pipe Company provided comprehensive support from the conceptual design phase, through manufacturing, delivery, and installation. Regular meetings and consistent communication ensured all stakeholders were up to date on production and delivery schedules. Representatives from the NWP Trenchless team were on-site during the initial push of both HDD drives to offer guidance and support and ensure a smooth installation process.
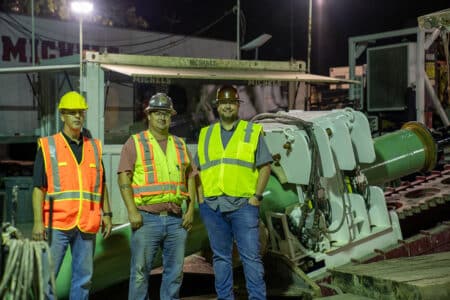
The successful installation of Permalok® HDD pipe under the East River marks a major milestone for the Champlain Hudson Power Express project and demonstrates how an innovative trenchless approach can overcome the challenges of utility construction in dense urban areas. The Permalok® system reduced the project’s footprint and improved construction speed and efficiency, helping stakeholders to meet ambitious project timelines while minimizing disruption to the city’s residents. As the state moves towards its renewable energy goals, this reliable underground transmission line will play a crucial role in delivering clean hydroelectric power to millions of New Yorkers, contributing to a more sustainable energy future.
For more information on this project, visit https://chpexpress.com/