Quality Assured: How a Robust QA Program Yields Project Success
Breaking Down Northwest Pipe Company’s Industry-Leading Quality Assurance Program
Northwest Pipe is committed to providing the highest quality products and services for our customers. We achieve this through our industry-leading quality assurance (QA) program. By continually monitoring and improving the performance of our quality management systems and objectives, our QA program ensures we consistently meet or exceed client expectations while maintaining lean manufacturing operations, reducing rework costs, and solidifying our market reputation.
Often paired with quality control, QA is a set of established procedures that maintain a desired level of quality in a service or product, and it touches every stage of the engineered steel pipe manufacturing process. Our QA program defines our production standards and outlines the steps necessary to achieve the quality and reliability that we’re known for at Northwest Pipe.
Benefits of our QA program include reducing manufacturing costs due to scrapped parts and returns, increasing efficiency, improving resource management, and increasing customer satisfaction by reducing product defects and maintaining project schedules.
Quality Assurance: A Team Effort
At Northwest Pipe, our QA team is involved in every step of the engineering and production process– from the corporate level, to the plant management level, to the production floor. As John Moore, Director of Quality Assurance for Northwest Pipe states, “Anybody and everybody who works at Northwest Pipe is responsible for quality. Every team member is empowered to call out and report any quality discrepancy.”
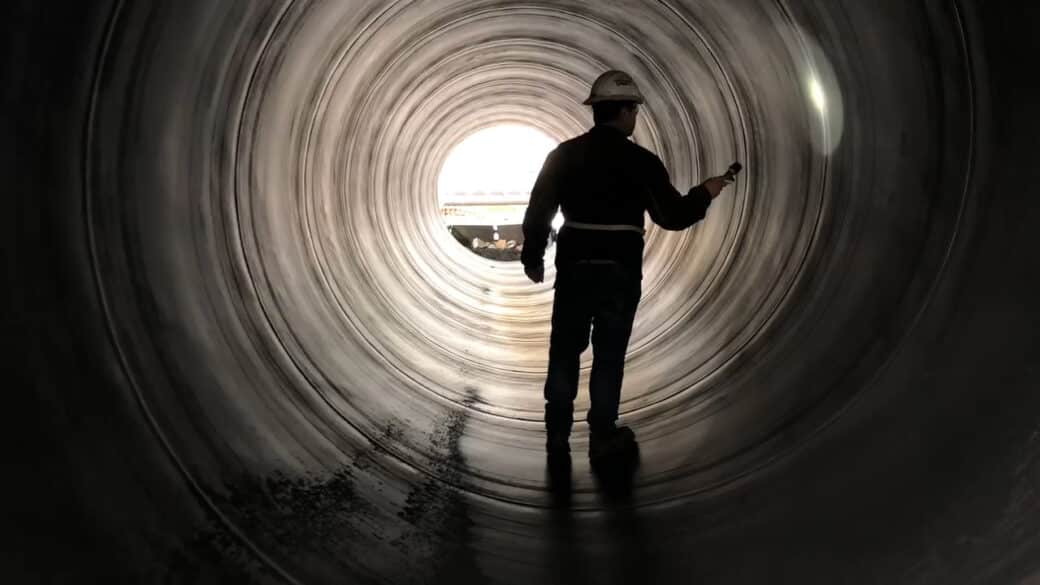
Our QA program starts with reviewing job specs, continues through production, and ends with field services to support installation contractors. We have strong productive relationships with project engineering teams and contractors, so we anticipate most testing and documentation needs prior to starting a job. We include a detailed spec package with each project, so all quality assurance notes and documentation are included at the end of a project.
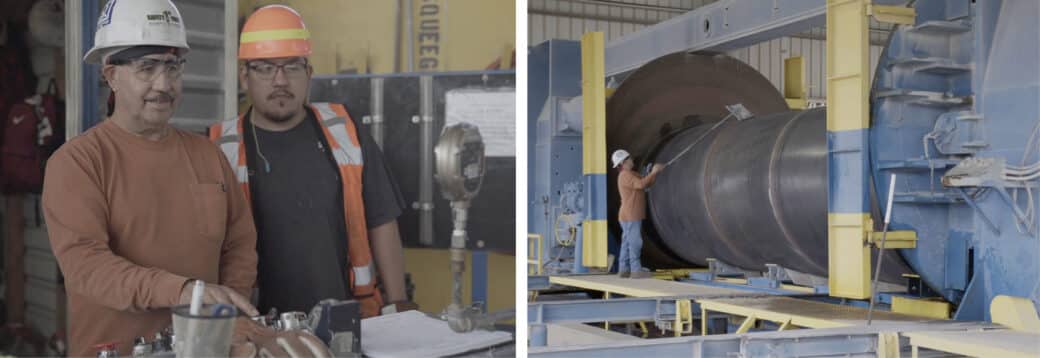
Product Tracking
Before production begins, the QA manager at each plant reviews the job specs and approves a coil requisite from the project manager. The QA manager will work with the project manager to approve the quality and type of material needed. Each coil is assigned a coil number to track it through production. When the team is ready to run a job, they match the job with the designated coil numbers. Similarly, our team assigns a number to each piece of pipe as it progresses through production. Our log notes when the pipe was milled, and the dates and person responsible for welding, hydro testing, coating, lining, and final product testing.
Inspection and Testing
Production of a single piece of C200 pipe passes through many on-floor inspection points. For example, a cement mortar-lined and polyurethane-coated piece will be inspected at the mill area, where the mill team monitors the spiral mills, welding areas, and the hydro testing areas. The QC team conducts the production weld tests, verifies repair welds, and certifies hydro testing. One of their most important tasks is verifying that all finished pipe has the correct diameters on each end so that the pieces join smoothly in the field.
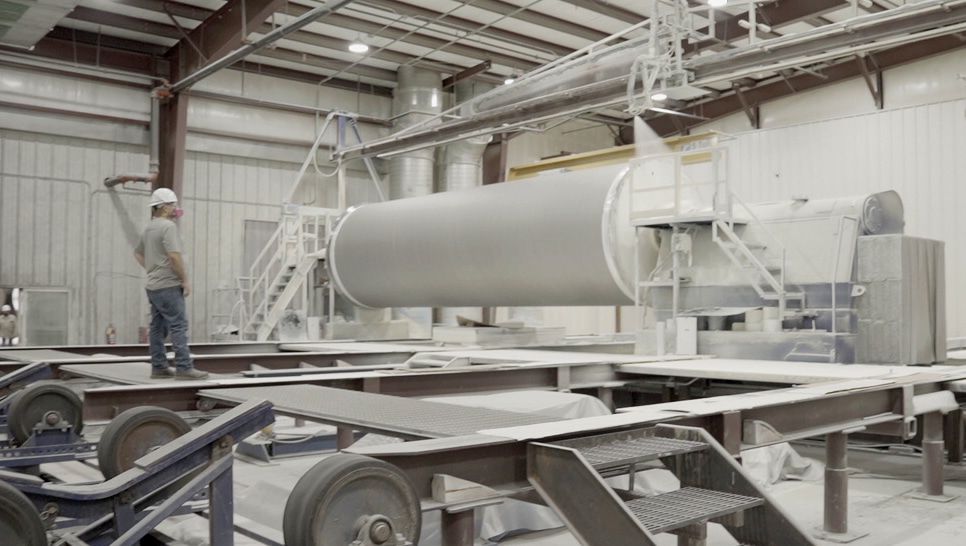
Lining inspectors perform compression tests to confirm anticipated quality and check the thickness of the lining. Prior to coating application, the coating quality control team confirms proper batch numbers and expiration dates to make sure they are correct. The coating team monitors environmental conditions, including humidity and temperature (surface and ambient), that can greatly affect the quality of sprayed coatings. They confirm holiday testing and check dried coating thickness and conduct adhesion tests as prescribed by AWWA. The fabrication team verifies the dimension of each modification and tests the quality of the welds using a variety of testing methods including, visual, penetrant (PT), and magnetic particle testing (MT). Other testing options include air testing, ultrasonic testing (UT), and x-ray (RT).
As the pipe prepares for shipping, each piece is given a ‘Mark Number’ that not only identifies where it is to be laid in the field but also tracks all production and testing information so that if an issue does arise, the team can look back at the manufacturing notes.
Certifications
Northwest Pipe Company is the only manufacturer of engineered steel pipe in the U.S. to hold a multi-site certificate of conformance (Certificate No. 33609) for ISO 9001:2015 for the design and manufacturing of welded, bare, lined, and coated steel pipe and fittings. In addition to our ISO 9001 certification, several members of our QA/QC and production staff also hold ASNT-TC-1A Level 1, 2 and/or 3 certifications in PT, MT, UT and/or RT. We have employees that have all three levels of NACE (National Association of Corrosion Engineers) certification for coating inspection and over 15 that are Certified Welding Inspectors (CWI), who are regulated, tested, and certified by the American Welding Society (AWS). All certifications are recognized worldwide.
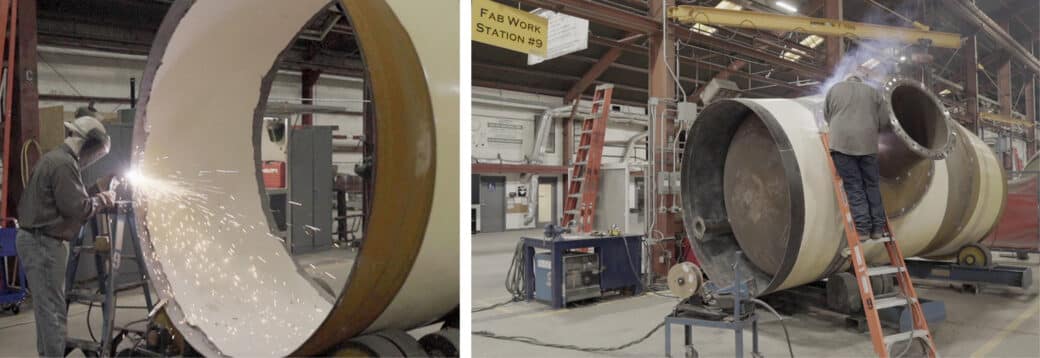
While every project is different, our commitment to quality remains the same. From first spec to final delivery, Northwest Pipe clients rely on the rigorous standards of excellence achieved through our robust and continually improving quality assurance program.