Magna Water District Manhole Rehabilitation
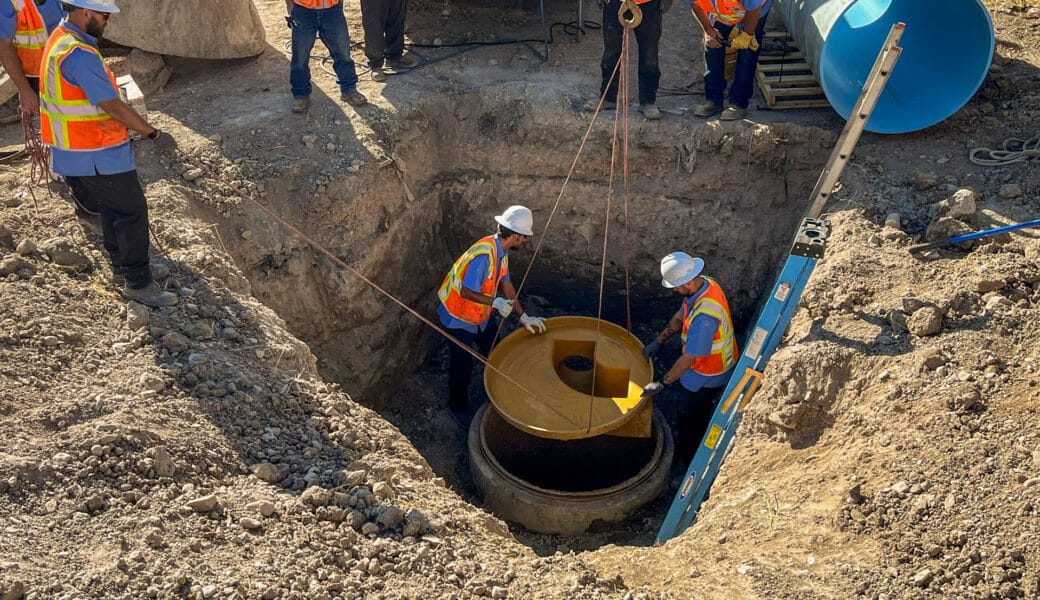
Specifications
Owner
Contractor
Engineer
Magna Water District, located in Salt Lake County, Utah, faced a unique infrastructure challenge when a severely corroded concrete manhole required rehabilitation in a location where bypass pumping was not feasible. The 48-inch manhole was exposed to a high concentration of caustic hydrogen sulfide gases due to poor ventilation, exacerbated by nearby construction activities. Earthwork and other debris covering the manhole lid clogged the vents, preventing gases from escaping. As a result, these corrosive gases accumulated inside the manhole and rapidly eroded the concrete structure.
Most available rehabilitation methods can only be performed under ideal conditions: dry, clean, and temperature-controlled environments, which typically require bypass pumping to maintain. However, a major highway separated the manhole requiring rehab from the next downstream manhole. Setting up a bypass over, under, or around the highway would have incurred significant costs, increasing exponentially with the project’s duration. Geneva Pipe and Precast’s Hybrid PVC Manhole System offered Magna Water District a permanent, structural rehabilitation solution that could be installed in a live sewer environment, eliminating the cost of bypass pumping and expediting the installation process.
The Hybrid PVC Manhole System used in this project consists of a base liner made out of Fiberglass-Reinforced Polymer (FRP), a 42-inch diameter by 115-inch depth PVC riser, and an FRP-lined flat lid with a 30-inch opening. The base liner includes 11.5-inch diameter inlet and outlet holes, and a channel with a 90-degree bend connecting the two. The engineering team at Geneva Pipe utilized a 3D scan of the existing structure to create a model that allowed for the design of a base liner that precisely fits the channel dimensions and preserves the hydraulic capacity of the manhole. The base liner is custom-manufactured from FRP material with minimal thickness, which reduces the hydraulic impact on wastewater flow during rehabilitation.
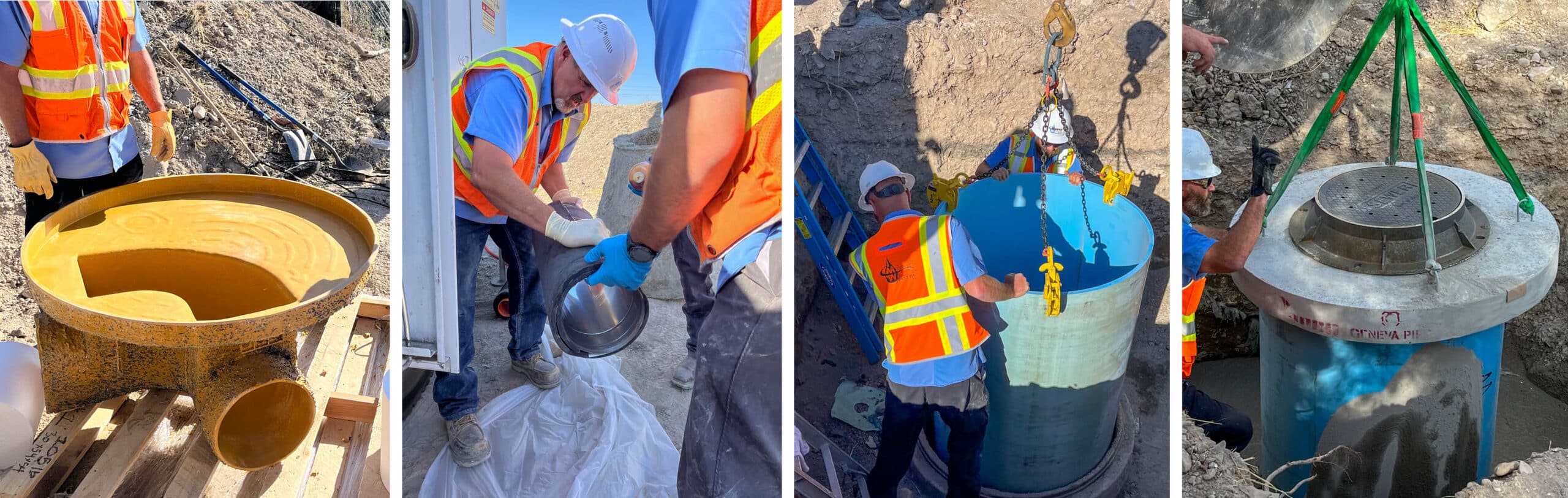
Installing the Hybrid PVC Manhole System follows a straightforward process that Magna Water District employees were able to self-perform, resulting in additional cost savings for the rehab project. First, crews excavated around the cone of the existing structure. Then, they modified the bench using saws and jackhammers to accommodate the base liner’s thickness before dropping the liner into place. This bench modification step can be eliminated or minimized by utilizing a base liner designed with near-exact (instead of exact) dimensions as the existing channeling, although the thickness of the liner may marginally affect the system’s hydraulic capacity.
After the base liner was in place, stainless steel compression sleeves were installed to connect the liner with the existing inlet and outlet pipes. These connectors create a mechanical and chemical bond that keeps the concrete structure out of contact with the wastewater, effectively preventing corrosive elements from causing further deterioration. Next, high-strength, high-flow grout was poured to anchor the liner in place and provide structural support for the base. Mastic was applied before stacking the PVC riser onto the base liner, ensuring a water- and gas-tight connection between the nested components. The annular space between the PVC riser and the existing manhole was then grouted. Finally, mastic was applied to the top of the riser before the FRP-lined lid was placed on top, and crews backfilled around the newly refurbished manhole.
Rehabilitation was successfully completed in under three days, including all excavation and installation work. Since this was their first experience using the Hybrid PVC Manhole product, the District wanted to take their time and involve the entire crew to familiarize them with the process in preparation for future installations.
The Hybrid PVC Manhole System offered Magna Water District a permanent and effective structural rehabilitation solution, resulting in substantial cost savings. By enabling crews to perform the work in a live sewer environment, it removed the need for bypass pumping, reducing project expenses and streamlining the installation process. This innovative approach not only addresses immediate corrosion concerns but also ensures maintenance-free service for decades, unlike temporary rehab methods such as field-applied coatings that require periodic reapplication. The project’s success demonstrates the Hybrid PVC System’s effectiveness as an innovative and permanent manhole rehabilitation approach for challenging cases where traditional methods are impractical, cost-prohibitive, or inadequate.